VST / VSH / VSE VS series recuperators
- Energy classes
- A
- B
- C
- D
- E
- F
- G
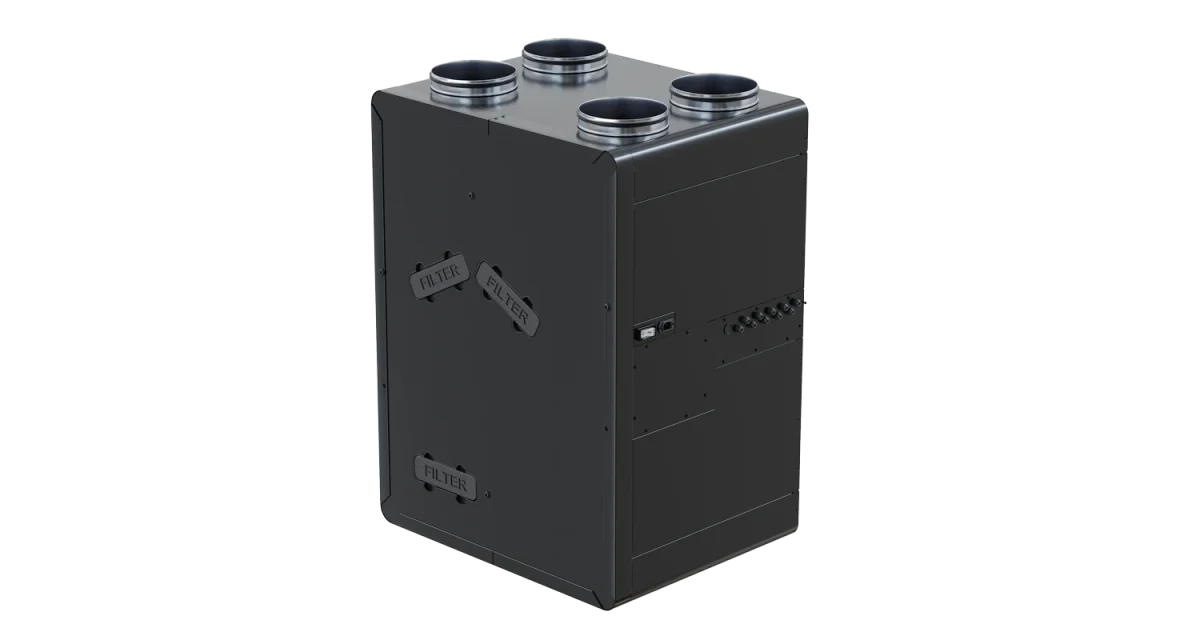
VST / VSH / VSE
VS series recuperators
- Modern EPP casing
- Temperature and moisture recovery*
- Energy efficient EC fans
- Innovative anti-freeze system
- Double filtration air supply
For Price list, please send inquiries to: export@v-k.pl
Check the product configuration options
Downloads
Construction of the recuperator
Height: 1031 mm
Width: 726 mm
Depth: 572 mm
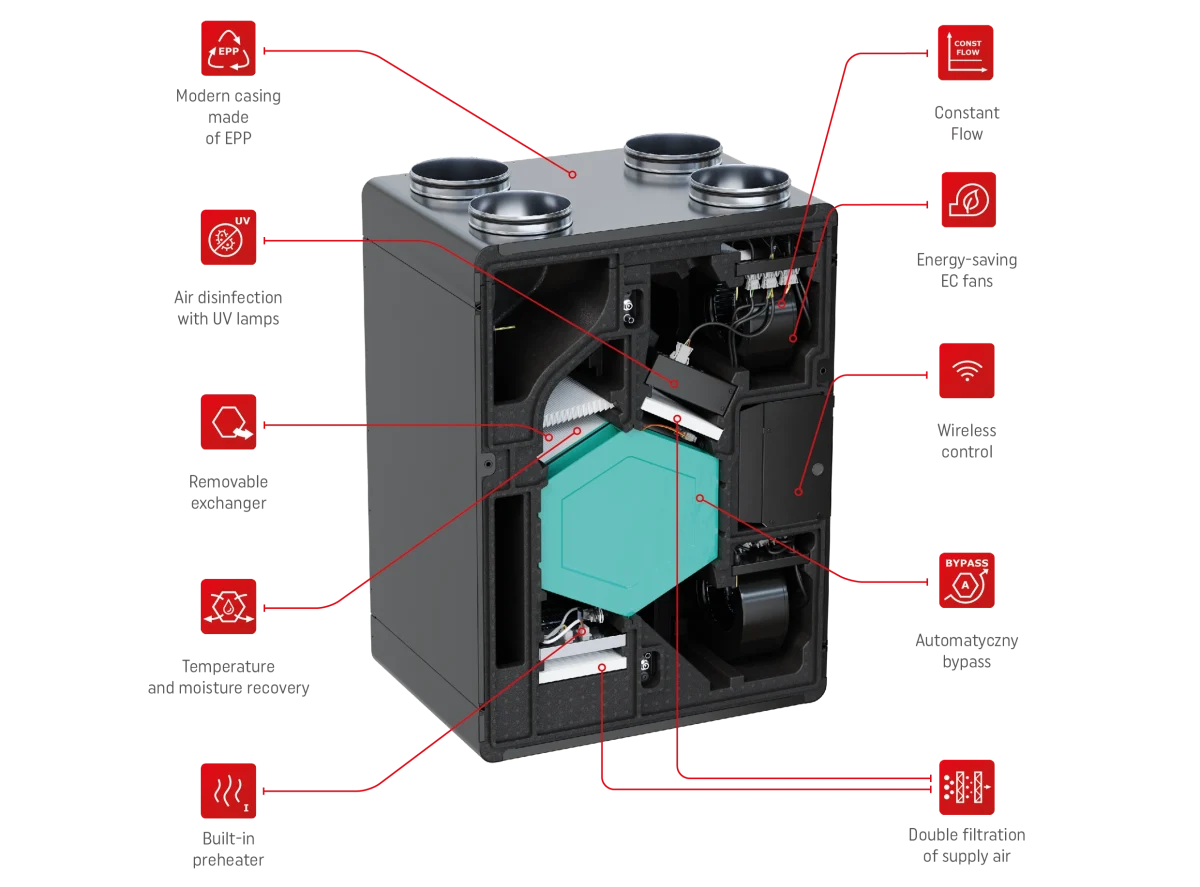
FreshAIR VS series recuperators are well suited for rooms where vertical ducting to the air handling unit is designed, as well as in boiler rooms and utility rooms with limited cubic capacity.
The casing made of extruded polypropylene (EPP) with a thickness of 40 mm provides optimal thermal and acoustic insulation.
Compact air handling units are equipped with a two-stage filtration system, an optional heater or cooler, and a temperature, hybrid or enthalpy exchanger. The standard Constant Flow (CF) system makes it easy to regulate the installation and guarantees a constant airflow regardless of atmospheric conditions or the dirtiness of the filters.
EQUIPMENT OF AIR HANDLING UNITS:
• temperature exchanger, enthalpy exchanger or hybrid exchanger*,
• built-in secondary heater or built-in water cooler*,
• energy-efficient EC fans with Constant Flow function,
• two-stage air filtration:
• ePM10 60% pre-filter (x2)
• anti-smog filter ePM1 55%
• automatic bypass,
• modern anti-freeze system,
• built-in PTC pre-heater,
• condensate connection stub,
• UV lamp disinfection system,
• controller with WiFi module,
• monochrome built-in touch panel or color wall-mounted touch panel*,
• humidity sensor or humidity sensor together with wall-mounted air quality sensor*.
* – Depending on the air handling unit model selected, see table.
ADDITIONAL COMPONENTS:
• a set of brackets for mounting the unit on the wall,
• console for mounting the unit on the floor,
• nipple fittings with gasket,
• reduction Ø 180/200 mm or Ø 180/160 mm,
• set of filters (3 filters),
• UV lamps set (2 pcs.),
• siphon,
• throttle actuator with return spring,
• heating cable with thermostat for condensate drain heating.
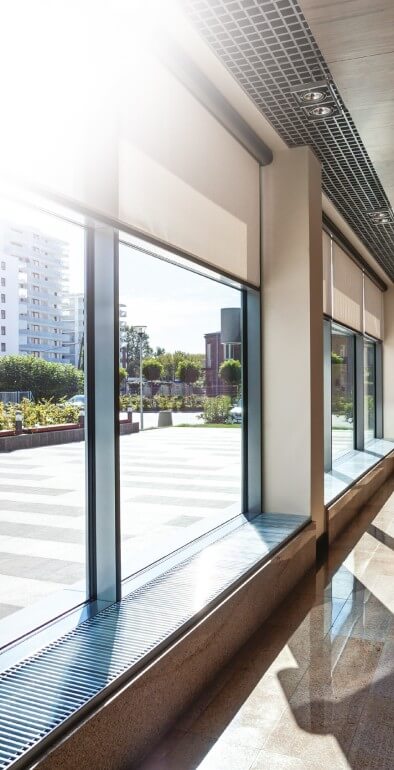
The most important features
Temperature and moisture recovery *
Available models from the VW series: VWT, VWH and VWE differ in the used heat recovery method . The heat exchanger, as a central element of the air handling unit, allows heat recovery from the exhaust air to the supply air. Classic temperature exchangers (VWT air handling unit) allow for sensible heat recovery, which depends solely on the temperature difference between the balanced airflows.
Hybrid and enthalpy exchangers differ in the amount of moisture recovery from the exhaust air.
Moisture recovery has dual benefits:
- Recovery of total heat (including energy contained in water vapor)
- Humidification of air supplied to rooms in winter
The flow of dry air into the rooms results in a decrease in comfort (coughing, sore throat, eye irritation) and it affects the rising of dust particles in the rooms.
* Not applicable to the VWT recuperator. Hybrid heat exchangers (VWH unit) and enthalpic heat exchangers (VWE unit), thanks to a special membrane, allow moisture recovery as well.
Automatic bypass
A bypass is an additional duct built into the recuperator that allows the intake air stream to bypass the heat recovery system. During the transitional and winter seasons, the recuperator allows heat recovery from the exhaust air. In summer, when the temperature of the outside air in the evening and night is lower than the indoor temperature, the heat recovery system can be bypassed. This will lower the air temperature in the house without the use of an air conditioning system.
Dual filtration of supply air
In collaboration with the Department of Indoor and Outdoor Air Quality of Lublin University of Technology, a supply air filtration system has been developed and tested to ensure air disinfection efficiency of min. 70% for three strains of bacteria (Micrococcus luteus, Pseudomonas fluorescens, Bacillus subtilis)*.
The used primary filter ePM10 (60%) allows to sift out coarse airborne dust, and the anti-smog filter ePM1 (55%) sifts out the finest dust with a diameter of less than 1 μm: viruses, bacteria, nanoparticles, soot.
Quick inspection and replacement of filters in VW series air handling units is possible after removing the plugs in the side cover of the unit.
* Test report No. 140/NN/2017 – Measurement of disinfection efficiency of UV modules.
High energy efficiency
Fans with EC motors have been matched to the airflows present in each recuperator, so that their operating point is in the area of high efficiency. Combining them with a dedicated controller and a variety of available sensors, made it possible to achieve an energy efficiency class A for various models.
Energy-efficient EC fans
Installed fans with EC motors are characterized by high efficiency and low energy consumption over the entire operating range. Modern, compact design allows to reduce heat generation, reduce motor vibration and extend the life of the device. The 0-10 V control signal allows smooth regulation of fan operation.
Constant Flow
Constant flow rate regardless of the dirtiness of the filters. Fans used in VW series air handling units are characterized by a built-in Constant Flow function, thanks to which the flow rate set by the user is maintained despite changes in pressure resistance in the system caused, for example, by dirtiness of the air filters. Equalization of supply and exhaust airflows ensures the highest heat recovery efficiency. Adjustment of the air flow rate is based on the user’s expected value – there is no need to determine the operating point based on calculations for the ventilation system.
Innovative antifreeze system
The water vapor in the exhaust air cools and condenses on the fins of the heat exchanger. When the temperature of the air directed to the ejector drops below 0°C, condensate freezes between the fins. Temperature exchangers are particularly susceptible to freezing – in the case of other types, due to moisture recovery, the amount of condensate is much smaller. The anti-freeze system developed for freshAIR+ air handling units combines automatic heating of the heat exchanger, preheating of the air flow and (in the case of very low outside temperatures) modification of the set air flows.
Why is the antifreeze system so important?
Studies conducted on the validity of anti-freeze systems have confirmed that the freezing of temperature heat exchangers at outdoor air temperatures is possible at as low as 0°C.
Freezing of condensate on the exchanger fins causes clogging of the spaces through which the air flows, limiting the air flow, which consequently leads to a reduction in heat recovery. Thanks to the use of a specially developed anti-freeze system, heat exchanger freezing does not occur in Verano recuperation units.
Removable exchanger
If necessary, it is possible to remove the heat exchanger and wash it under warm running water. However, this is recommended by the manufacturer only in special cases-the heat exchanger is protected from dirt from outside and dirt from indoors by a 2-stage filtration system.
Built-in PTC preheater
The PTC preheater used is characterized by a stable, modular design, low flow resistance and uniform heating of the air stream. The temperature sensor used reduces energy consumption and protects the air handling unit from overheating.
Built-in secondary heater or cooler *.
For the sake of users’ thermal comfort, each air handling unit can be equipped with a secondary heater or a cooler with a condensate pump. The choice of the variant depends on the design of the ventilation system and the expectations of the investor. The secondary heater can be supplied by the agent of the central heating system, while a chilled water system is required to supply the cooler. Additional equipment is installed inside the housing of the air handling unit – there is no need to prepare a special section of the installation, so the decision to purchase additional equipment can be made already at the stage of system operation.
The connection to the central heating or chilled water installation is made by means of flexible pipes terminated with a half-screw. The automation system allows the connection of ON-OFF, three-position or 0-10V controlled actuators. In addition, it is possible to steer a circulating pump or an authorization signal for the operation of a central heating boiler or a chilled water unit using the control panel. Dedicated balancing valves, three-way or four-way, guarantee the achievement of the assumed design flow of the heating medium or chilled water.
*Built-in secondary heater or chiller is available on selected AHU models.
Remote operation via computer or smartphone
The controller was designed specifically for VERANO freshAIR+ recuperators. It transparently provides access to all functions and settings of VW series recuperators. It allows remote control of the air handling unit’s operation with the help of a web application available in a web browser or an application for tablets and smartphones available for Android and iOS.
The controller also allows recording data on the operation of the air handling unit in real time. The data is used during service inspections and allows for quick detection of irregularities in the operation of the unit. The controller is available in a version with a built-in, monochrome panel with buttons or in a version with a wall-mounted, color touch panel.
Possibility of connecting PM2.5; PM10; CO2; RH * sensors.
In addition to temperature sensors, you can also connect to the controller relative humidity sensor, CO2 concentration sensor, air quality sensor (PM10 and PM2.5).
Cooperation of the controller with GWC
It is possible to control the pump of the glycol ground heat exchanger circuit, which brings the medium heated in the ground to the finned heat exchanger located on the intake duct.
Modern casing made of EPP
Recuperator casings are made of foamed polypropylene, which forms the structure of the individual recuperator components. The production process is subject to strict requirements and is carried out in accordance with the ISO IATF 16949 and ISO 9001 quality management system, as well as the ISO 14001 environmental management system. The material from which the casings are made is 100% recyclable.
High thermal and acoustic insulation
The use of foamed polypropylene with a thickness of 40 mm provides excellent thermal and acoustic insulation of the device.
Lightweight casing design
Tailored parts, made with the help of injection molds, guarantee airtightness unattainable by classic sheet metal casings, moreover, the structure of the material guarantees the low weight of the device. It is also possible to make a recuperator with a casing completely covered with a steel sheet.